Understanding the Basics and Applications of Plastic Extrusion in Modern Production
In the world of modern-day production, the technique of plastic extrusion plays an instrumental role - plastic extrusion. This detailed procedure, involving the melting and shaping of plastic through specialized dies, is leveraged across various industries for the development of diverse items. From auto parts to consumer goods product packaging, the applications are large, and the potential for sustainability is just as impressive. Unwinding the basics of this process reveals truth convenience and potential of plastic extrusion.
The Basics of Plastic Extrusion Process
While it might show up facility, the principles of the plastic extrusion procedure are based on relatively uncomplicated concepts. It is a production procedure where plastic is thawed and afterwards shaped into a continuous profile via a die. The raw plastic material, frequently in the type of pellets, is fed right into an extruder. Inside the extruder, the plastic goes through heat and pressure, causing it to melt. The molten plastic is then required with a designed opening, understood as a die, to form a long, continuous product. The extruded item is cooled and afterwards reduced to the preferred length. The plastic extrusion process is extensively made use of in numerous industries as a result of its efficiency, flexibility, and cost-effectiveness.
Different Kinds Of Plastic Extrusion Strategies
Structure upon the basic understanding of the plastic extrusion procedure, it is needed to discover the numerous strategies included in this production approach. Both key techniques are profile extrusion and sheet extrusion. In account extrusion, plastic is melted and developed into a continuous account, often made use of to create pipes, poles, rails, and home window structures. In comparison, sheet extrusion develops huge, level sheets of plastic, which are generally more refined into products such as food product packaging, shower drapes, and auto parts. Each technique needs specialized machinery and exact control over temperature and pressure to make sure the plastic keeps its form during air conditioning. Understanding these strategies is essential to making use of plastic extrusion properly in contemporary manufacturing.
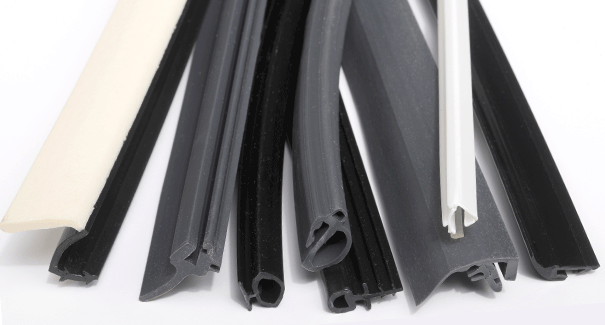
The Duty of Plastic Extrusion in the Automotive Market
A frustrating majority of parts in contemporary cars are items of the plastic extrusion procedure. This Home Page procedure has revolutionized the automotive sector, changing it right into a much more efficient, economical, and flexible manufacturing sector. Plastic extrusion is primarily used in the manufacturing of numerous auto elements such as bumpers, grills, door panels, and dashboard trim. The procedure supplies an attire, constant output, making it possible for producers to produce high-volume get rid of excellent precision and very little waste. The lightness of the extruded plastic components contributes to the total reduction in vehicle weight, improving gas effectiveness. The durability and resistance of these parts to heat, cold, and effect boost the long life of cars. Therefore, plastic useful source extrusion plays an essential role in vehicle production.

Applications of Plastic Extrusion in Durable Goods Manufacturing
Beyond its substantial effect on the automotive industry, plastic extrusion proves similarly effective in the realm of customer products manufacturing. The adaptability of plastic extrusion enables suppliers to develop and create complex forms and dimensions with high accuracy and efficiency. The versatility, adaptability, and cost-effectiveness of plastic extrusion make it a favored option for many customer items producers, contributing substantially to the market's growth and innovation.
Ecological Effect and Sustainability in Plastic Extrusion
The prevalent use plastic extrusion in making invites scrutiny of its environmental implications. As a procedure that often makes use of non-biodegradable products, the environmental impact can be considerable. Energy intake, waste manufacturing, and carbon exhausts are all issues. Industry improvements are boosting sustainability. Efficient equipment decreases power usage, while waste management systems reuse scrap plastic, reducing raw product needs. In addition, the development of naturally degradable plastics provides a more eco-friendly alternative. In spite of these improvements, further technology is required to minimize the ecological impact of plastic extrusion. As culture leans in the direction of sustainability, makers must adapt to continue to be viable, stressing the significance of continual research study and advancement in this field.
Conclusion
In verdict, plastic extrusion plays a critical function in click resources modern manufacturing, particularly in the automotive and consumer products markets. Understanding the fundamentals of this process is vital to optimizing its applications and advantages.
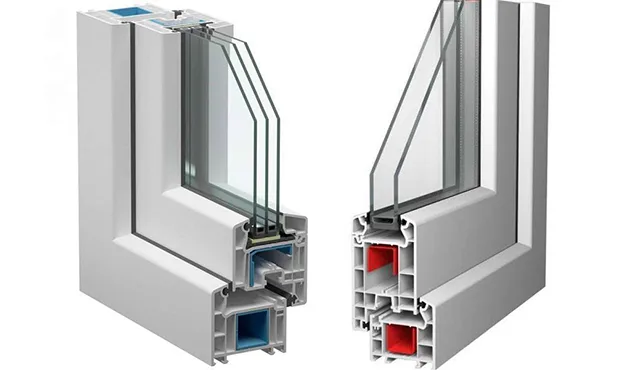
The plastic extrusion procedure is extensively used in different sectors due to its cost-effectiveness, efficiency, and convenience.
Structure upon the fundamental understanding of the plastic extrusion procedure, it is essential to check out the different strategies included in this manufacturing technique. plastic extrusion. In contrast, sheet extrusion develops large, level sheets of plastic, which are typically more refined into items such as food product packaging, shower curtains, and car parts.An overwhelming majority of components in contemporary vehicles are items of the plastic extrusion procedure